What is a company’s steering process, and how can it be improved?
Steering a company is a complex and essential task for the success of any organization. Whether for a small company or a large multinational, planning and implementing effective strategies are necessary to achieve set objectives and ensure sustainable growth.
In this article, we’ll delve into the details of the business’ steering process and examine the key factors involved. We’ll explore the different types of steering strategies, the elements present on a process map, and the different factors taken into account.
Whether you’re an entrepreneur, a senior executive, an investor or simply interested in how a business works, this article will provide you with a comprehensive and instructive overview of a company’s steering process.
What is a process?
In business, a process can be defined as a sequence of related activities that are carried out to achieve a specific objective. Processes can be used for a variety of business functions, such as production, project management, human resources, accounting, and many others.
A process can be seen as a way of standardizing activities to ensure consistent execution and quality. Processes are often described in procedural documents and can include steps, responsibilities, rules, and deadlines.
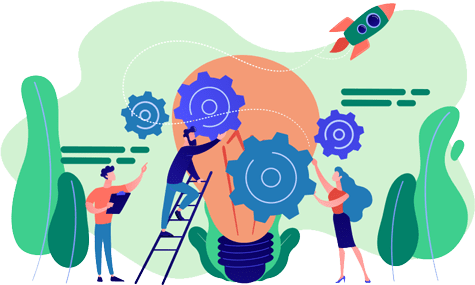
Processes are important for improving efficiency, productivity and capability. They also help reduce costs by avoiding errors and waste. In addition, processes help facilitate collaboration between team members by clarifying roles and responsibilities.
Processes can be improved over time through techniques such as process analysis and optimization, which identify inefficiencies and opportunities for improvement. There are many different types of process, which can be classified into several categories.
What are the different types of processes (or macro-processes)?
Operational or realization processes
There are many operational or realization processes in a company, which can vary according to business sector and business objectives. Here are a few common examples:
Production: Concerns the manufacture of physical products, from the receipt of raw materials to the dispatch of finished products.
Project management: The planning, execution and monitoring of projects, ensuring that projects are delivered on time, within budget and with satisfactory quality.
Customer service: Providing excellent service to customers, meeting their needs and solving their problems.
Human resources management: Personnel management, from recruitment to performance measurement and ongoing training.
Marketing and sales: Promoting the company's products or services to prospects, ensuring that products are marketed effectively and that sales are closed.
Supply chain management: Control of the entire procurement process, from planning to product delivery.
Financial management: Controlling finances, ensuring that expenditure is controlled, income maximized and accounts kept up to date.
These processes can often be subdivided into sub-processes, each with its own steps, responsibilities and rules.
Operational or execution processes
Support processes are those that provide services or support functions to help processes run efficiently. Here are some common examples of support processes in business:
Quality control: Quality assurance and quality control, which ensure that products or services meet standards and requirements.
Security: Controlling security risks and threats to protect assets and employees.
Information technology management : Management of IT systems, including planning, installation, maintenance and upgrading of software and hardware.
Logistics: Organizing the flow of raw materials and finished products between the company's various sites and to customers and suppliers.
Learn more about ERP for logisticskeyboard_returnHuman resources: Managing payroll, benefits, regulatory compliance and corporate HR policy.
Purchasing: Acquisition of goods and services, including sourcing, contract negotiation and supplier relationship management.
These support or back-up processes are essential to ensure that operational approaches work efficiently and consistently. They provide critical support for risk measurement, activity coordination and regulatory compliance.
Management processes
Management processes are those used to direct and manage the company as a whole. Here are some common examples of management or direction processes:
Strategic planning: defining the company's vision, mission and strategies, and planning the allocation of resources and priorities for the short and long term.
Performance management: assessing the success of the company and its employees, and implementing action plans to improve performance.
Risk management: managing the risks that can affect the business, in particular by identifying, assessing and mitigating risks.
Change management: planning, implementing and monitoring organizational change, in particular by ensuring that employees are ready to cope with the changes.
Communication: Internal and external communication, including stakeholder relationship management, brand management and internal communication between employees.
Financial management: including financial planning, budgeting, cash, cost and investment control.
These management or executive processes are essential to ensure that the company is run effectively, ensuring that objectives are achieved, risks are managed and employees are aligned with the company’s vision and mission.
What are the elements of a company’s process map?
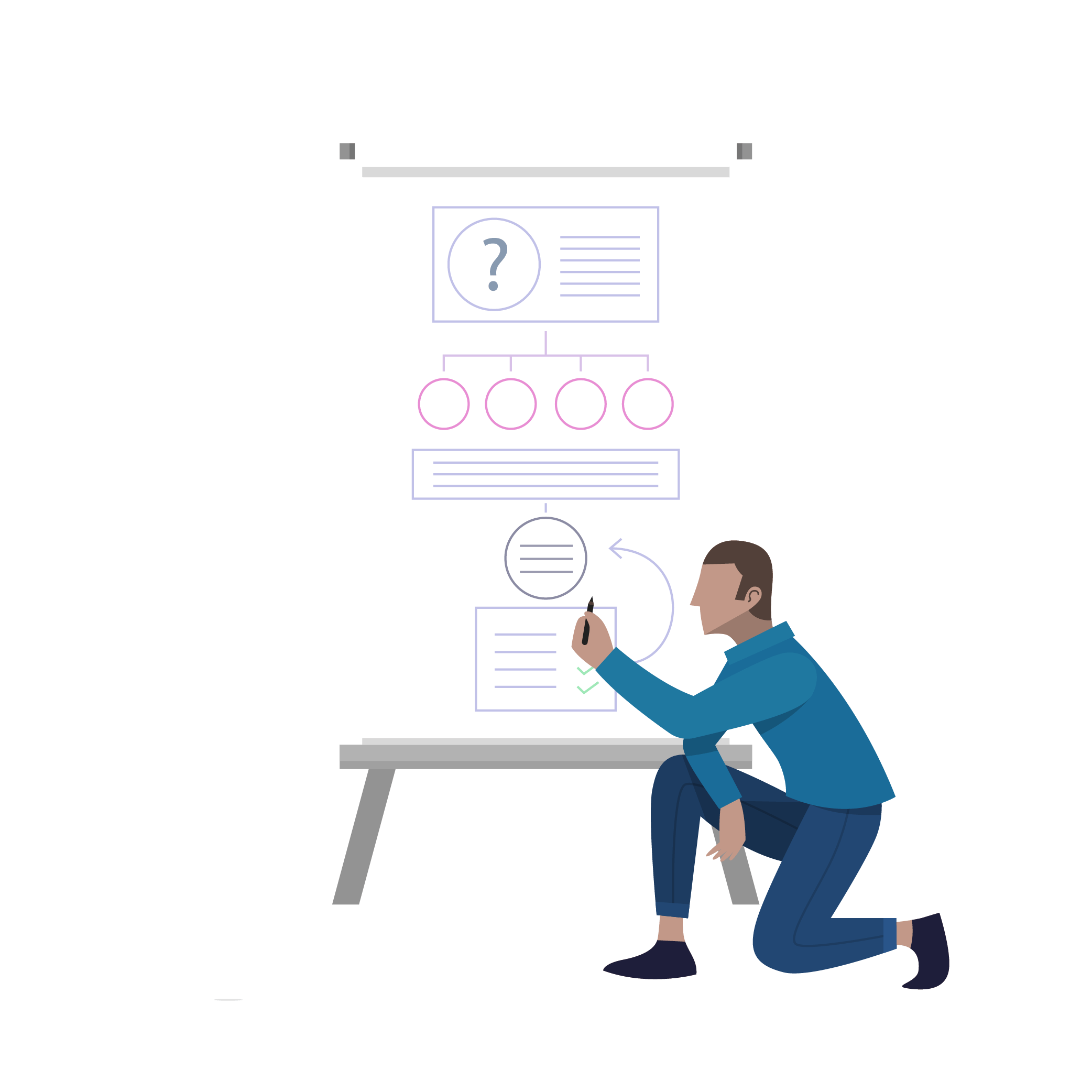
A process map is a visual representation of a company’s key processes, and how they interact with each other. Elements commonly found on a process map include:
• Processes: these are the specific activities within the company. Processes can be represented as blocks on the map.
• Inputs and outputs: the raw materials, information, capacities or other factors that go into the operation, and the results or products that come out. Inputs and outputs can be represented as arrows on the map.
• Roles and responsibilities: the people or teams responsible for carrying out tasks within the organization. Roles and responsibilities can be represented by symbols or codes on the map.
• Performance indicators: these measures assess the effectiveness and efficiency of the process, such as cycle time, defect rate, cost or customer satisfaction. Success indicators can be represented as graphs or tables on the map.
• Process links: how different processes interact to produce results. Process links can be represented as arrows or connectors on the map.
A process map may vary according to the complexity and size of the company, but these elements are generally present to help understand how the different processes work together to achieve the desired results.
What types of factors are taken into account by the steering process?
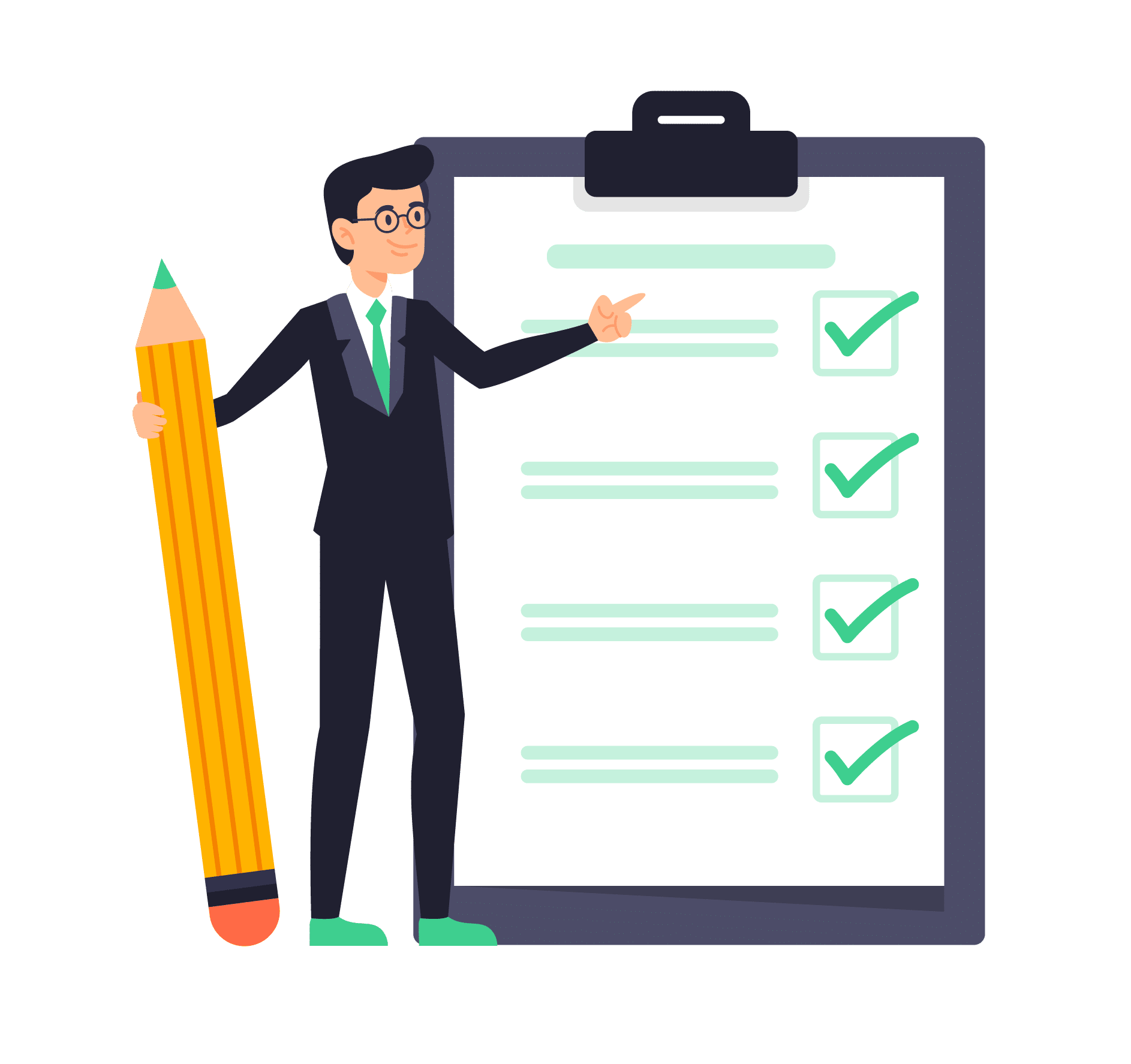
The steering process takes into account a number of key factors to measure and manage strategic performance, including:
• Performance indicators: these are measures used to monitor and evaluate performance, such as sales, margins, customer satisfaction, costs, delivery times, quality, safety and regulatory compliance.
• Strategic objectives: these are long-term plans, such as market expansion, innovation, cost reduction or quality development.
• Action plans: these are plans for achieving strategic objectives, such as marketing, production, HR or investment plans.
• Budgets and resources: these are budgets allocated to achieve action plans, as well as resources, such as employees, raw materials, machines or technologies.
• Risks and opportunities: these are factors that may affect the achievement of results, such as market, operational, financial or compliance risks, or growth opportunities.
• Past performance: this refers to the company's track record, which can be used to assess strategic trends, strengths and weaknesses.
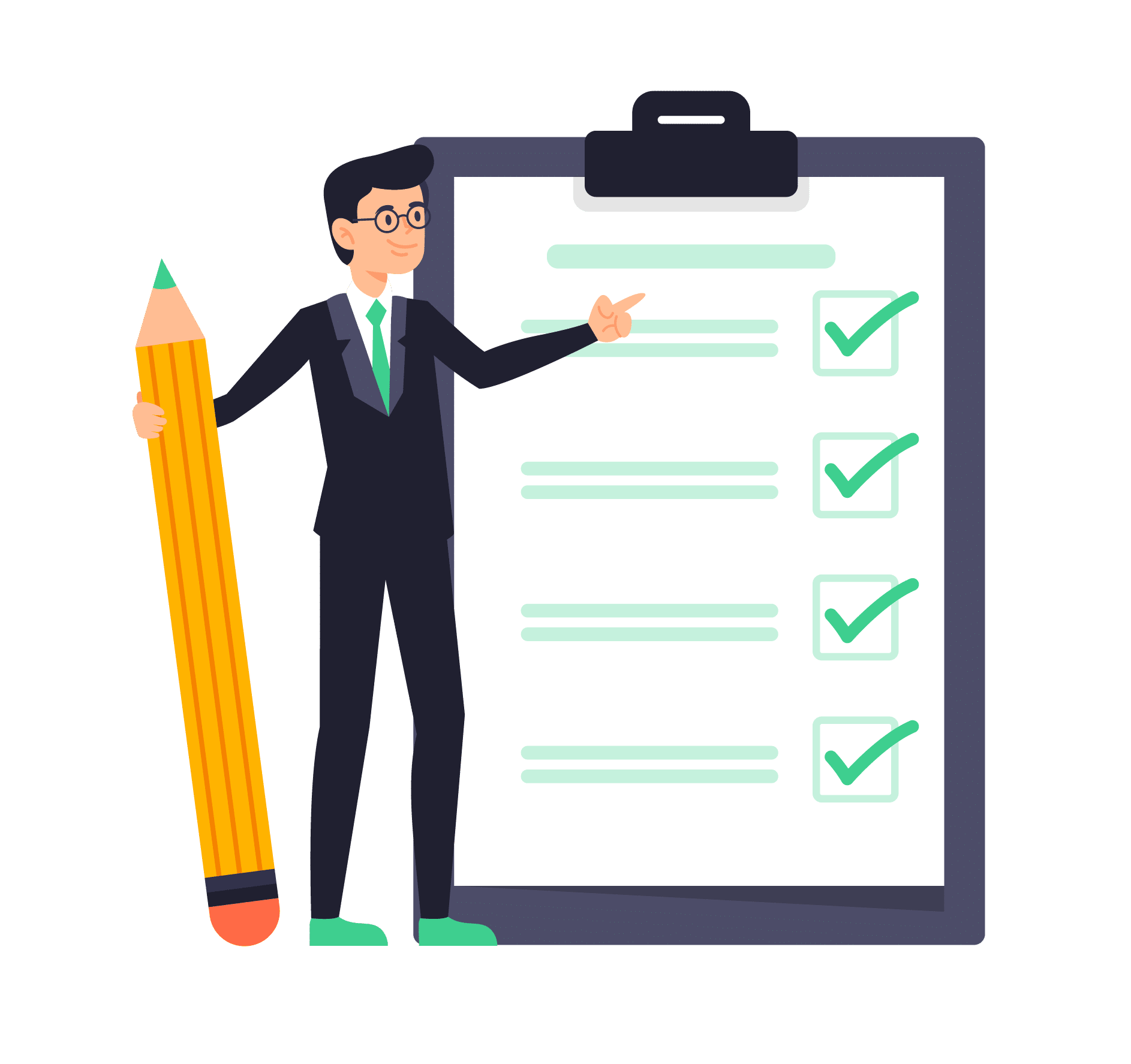
By taking these factors into account, the steering process enables the company to monitor and measure its performance, make informed strategic decisions and adapt to changes in the market and business environment.
How to identify processes according to different Afnor standards?
AFNOR (French Normalization Association) has published several standards relating to process management. One of these is NF EN ISO 9001. It describes the requirements for setting up a management system developed within a company. In particular, it recommends :
Identify key processes based on customer and stakeholder requirements.
Define KPIs for each key process.
Measure and monitor process success using performance indicators.
Implement continuous improvement actions to enhance profitability.
What does setting up a process management system mean for your company?
Implementing a process management system can have many impacts on a company, depending on the scope and complexity of the system in question. Here are some of the main effects:
• Improved quality: with an overview of the company's processes, it becomes easier to identify problems and bottlenecks that may affect product or service quality. With a process control system, managers can implement measures to remedy problems and thus improve quality.
• Cost optimization: process management can also help control costs by identifying non-essential or redundant steps in the company's processes. By eliminating these steps, costs can be reduced, which can have a significant impact on profitability.
• Enhanced competitiveness: by improving quality and reducing costs, a company can become more competitive in the marketplace. Process management can also help to improve responsiveness, by enabling problems to be detected more quickly and corrective action to be taken.
• Improved communication: process management can also foster better communication between different teams. With an overview of processes, it becomes easier to understand how different teams interact with each other, and to better coordinate actions.
• Alignment with strategic objectives: steering can help align a company's actions with desired results. By defining key performance indicators (KPIs) for each process, you can ensure that actions are consistent with your strategy.
All in all, implementing a process management system can have many benefits, including improving quality, optimizing costs, boosting competitiveness, enhancing communication, and aligning with strategic objectives.
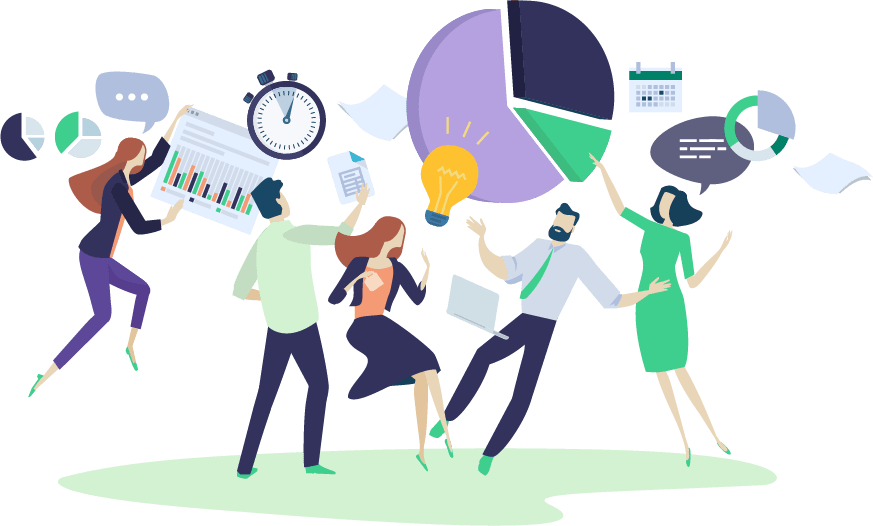
Find out how our ERP can help you improve your company’s performance
An expert will contact you shortly to discuss your project.